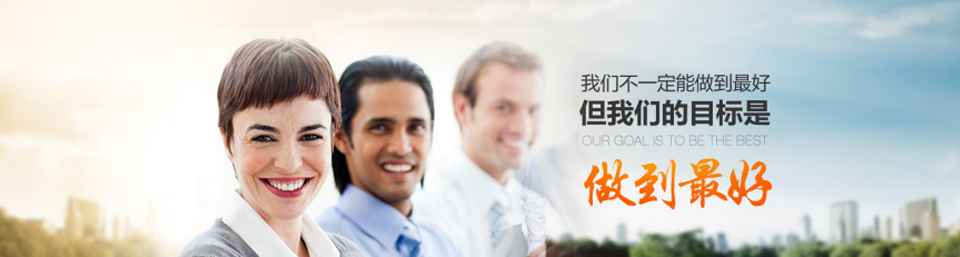
电解槽用智能打壳气缸
电解槽用智能打壳气缸是应用于铝电解生产的工业自动化控制设备。在铝电解生产过程中电解槽需要不断地消耗原料,从而通过电解生产出铝水。但由于生产设备的特殊性结构,加入的氧化铝原料过程是间歇性的,而加入口在一段时间内很容易自我封闭 , 在表面形成很硬的壳,只有通过专业的打孔设备打开壳孔,才能将氧化铝加入,这种专业的打壳设备称之为打壳气缸。由于打壳气缸所处的环境是高污染、大磁场、高温的,对打壳气缸的设备和器件适用性提出了较高的要求,同时还需满足铝电解槽的加料工艺需求。
目前国内外铝行业采用大型预焙电解槽进行电解生产,在预焙铝电解槽中均采用中间下料的生产模式,对于中间下料的铝电解槽,电解槽上部衍架上的打壳气缸是铝电解生产的关键设备,它由微机自动控制打壳下料之间的协调与配合,完成电解铝正常生产。
在铝电解生产中覆盖在电解质上的氧化铝很容易在表面形成结壳,对于自动加料的生产设备通过打壳气缸打开壳口,按需加入氧化铝连续生产,传统的打壳气缸在每次下料前打壳。由于铝电解生产的特殊性,每次下料时的结壳状况不同,而且电解槽的工作状态不完全恒定,所以加入氧化铝的时间间隔也各不相同,对于特殊情况下还会出现停止加料的时期,同时在不同的生产工艺条件下,结壳的厚度与硬度也不尽相同,如果每一次下料都进行高压打壳,会大量浪费了打壳能源。传统打壳气缸没有壳面检测功能,每次打壳不管壳面状况,都按大行程动作,将锤头伸入电解质中,造成锤头的腐蚀、缩短、锤头毡包等,引起以后的打壳长度不够和壳头变形导致的料口狭小,造成堵料。同时被电解质腐蚀掉的壳头还会对铝水造成杂质污染,影响铝水质量。因此研究一种按需打壳,壳头不伸入电解质的智能打壳气缸,不但可以节约能耗,同时可以提高生产铝水的质量。
现在铝电解槽普遍使用的是普通打壳气缸,虽然市面上有各种类型的智能气缸,如铝用节能气缸、高温节能型气缸、多段式气缸、降噪打壳气缸等。铝用节能气缸,在接收到控制系统的打壳命令后,先进行试探性打壳,如若不能成功,则再进行加压打壳或高压打壳,不能提前预判结壳壳面的状况 ;而高温节能型气缸,是先进行压壳,如若不能成功,则再进行定压打壳 ;多段式气缸是,在气缸上设置不同的限位,采用分段式压力进行打壳,不同的压力达到不同的壳面位置,尽量避免打壳锤头被浸入电解质中 ;而降噪打壳气缸的主要特点是,根据检测到壳面采用逐步加压,压壳或再冲击打壳方式打壳,以减小打壳的噪音。
现有铝电解槽采用的打壳气缸,不管是节能型打壳气缸,还是降噪型打壳气缸,他们都有一个共同的特点是,在接收到槽控系统发出命令后,不能预判壳面状况,直接进行打壳,不能根据工艺和生产的特点来进行打壳。它们在接收到控制系统的打壳命令后,先进行试探性打壳,如若不能成功,则再进行加压打壳或高压打壳,只是打壳的方式分为低压、高压、或变压力型打壳。由于电解生产壳面的固有特性,和电解生产过程中的下料的不确定性,每次壳面状况不同 ;这样不断试探性打壳,不但造成了打壳能源的浪费,同时也无形地延迟了下料的时间,可能会造成电解槽的短时供料不足,带来效应。由于每次打壳到打壳完成的时间各不相同,破坏了控制系统的下料预测模型,造成了下料的不确定性,给生产带来了更大的坏处,浓度控制不精确,效应频发等问题。传统打壳气缸没有壳面检测功能,即使有不同的限位,也是固定的,不能根据每次不同的壳面高度进行自动调整,每次打壳不管壳面状况,都按固定或大行程动作,经常将壳头伸入电解质中,造成壳头的腐蚀、缩短、壳头毡包等造成以后的打壳长度不够和壳头变形导致的料口狭小,造成堵料。
为了解决上述问题,郑州博亿开源自动化设备有限公司提供一种一种电解槽用智能打壳气缸。
电解槽用智能打壳气缸大特点是自动检测壳面,当多次打壳以后,系统会在预测出下次打壳时的壳面情况,并决定打壳方法和打壳行程。铝电解生产过程中正常情况下的打壳基本上是加压打壳,而只有对于刚启动的电解槽、以及有堵料现象的电解槽或较长一段停止加料的电解槽,才会出现使用冲击打壳的方法。加压打壳一般为冲击打壳的三分之一的压力,不但很好地节约了能源,同时也降低了打壳噪音。同样本产品的免倾入电解液的功能,也强于市面上的智能气缸。原因是 :打壳的行程是依照电解槽的生产状况自动调整的,所以更好地减少了锤头的腐蚀与磨损。
另一特点是:既可以当作智能气缸,也可以当作普通气缸使用;不但可以当作智能气缸使用于新建电解槽,也可适用于已生产的电解槽,用本产品直接代替原有的气控柜和打壳气缸两者即可。
图中:1-减压阀,2-两位五通电磁阀,3-压力传感器 ,4-压力传感器,5-高低限位开关 ,6-高低限位开关,7-打壳锤头,8-打壳气缸,9-PLC控制器,10-槽控机,11-连接电缆,13-压缩空气总管。
具体实施方式:
如图所示,本新型电解槽用智能打壳气缸包括设置在电解槽加料口上方的活塞杆端连接有打壳锤头7的打壳气缸8,打壳气缸的两个进出气口通过管路分别与两位五通电磁阀2的相应接口相连,两位五通电磁阀2通过减压阀1与压缩空气总管13相连接;在打壳气缸的两个进出气口处分别设置有压力传感器3、4,在打壳锤头伸缩运动的上、下行程止点处分别设置有限位开关5、6 ;压力传感器、限位开关、减压阀以及两位五通电磁阀的控制接口均通过连接电缆11与PLC控制器的相应接口连接,PLC控制器通过连接电缆11与槽控机通讯连接。
打壳锤头的锤杆上设置有与限位开关相配合的凸状触点;压力传感器为GB-3000A压力变送器,压力变送器采用管接式安装,量程为0~1.6MPa,输出4~20mA, 采用供电24VDC;减压阀为带有过滤调压阀气源处理三联件的AC5000-10-减压阀;两位五通电磁阀的型号为BJK25-15;
本产品配置了一个工业控制器,工业控制器直接采集压力传感器、打壳限位传感器(限位开关)的输出信号,并控制打壳的执行,同时工业控制器具有打壳命令输入口和打壳反馈继电器口,以及485通讯口,工业控制器可选择与槽控机或气控柜相连。
工作原理如下:当PLC控制器接收到槽控机发出的打壳命令信号,气缸加以2bar的压力进行打壳,气缸伸出,碰到壳面后阻力增加,如果壳面很薄在2bar的压力下可以打开壳面;否则若不能打开壳面,槽控机控制气缸缩回,并以高压冲击打壳,在设定的次数可打开壳面的,PLC控制器向槽控机反馈打壳完成信号,否则反馈打壳故障报警信号,要求人工处理。在正常情况下,壳面较薄,低压打壳即可打开壳面,对于较长时间间隔后的打壳,壳面较厚,但可以通过高压冲击打壳完成。当槽控机接收到打壳完成命令后,就可开始下料,一次打壳结束。
打壳的壳面判别方法,当锤头伸出遇到壳面时,阻力增加,压力曲线斜率发生变化,当壳面较薄时,压力曲线斜率变化不大;但当壳面较厚时,压力曲线斜率变化很大,即出现拐点,通过比较曲线的斜率和拐点情况,即可判断壳面的薄厚。
PLC 控制器的工作原理如下:控制器记录每次打壳的时间间隔,以及壳面的薄厚状态,并通过预测控制算法,计算出本次的壳面状况,与实际打壳的壳面薄厚作比较,不断总结不同时间间隔下的壳面情况,并修正本次打壳的打壳压力。这样在接受到打壳命令后,通过预测控制算法,就可逐步确定打壳的压力,为了简化预测,可采用分段式压力控制参数。
通过以上的方法我们在400KA电解槽使用取得了节能压缩空气约64%的效果,约50%以上的打壳为低压打壳,打壳噪音降低了50%以上。